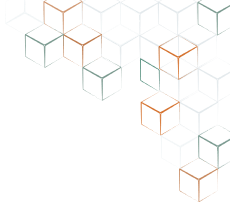
PRESSURISED ALKALINE WATER ELECTROLYSIS
After more than a decade of dedicated research and development, Green Hydrogen Systems (GHS) has developed an advanced electrolysis solution, designed to address the complex challenges in the green energy transition.
OUR JOURNEY TO PRESSURISED ALKALINE
Overview: GHS began its journey in hydrogen production by testing and deploying an atmospheric electrolyser designed for a hydrogen-powered train.
Details: This initial setup provided critical insights, leading to several improvements such as internal pressurisation to eliminate the need for mechanical gas compressors, enabling modular factory assembly, and the use of standardised components.
Outcome/Impact: These enhancements would improve serviceability, minimise downtime, and set the stage for future advancements in electrolyser technology.
.png?width=90&height=224&name=TestingDeployment%20of%20Pressurised%20Alkaline%20Electrolyser%20(10).png)


2008: Testing/Deployment of Atmospheric Alkaline Electrolyser
Overview: GHS tested and deployed a PEM electrolyser with a 5.5 kW capacity, producing 1 Nm³/hr of hydrogen.
Details: With an operating efficiency of 62 kWh/kg H₂, the PEM electrolyser generated hydrogen at 50 bar(g) pressure but faced high production costs due to its reliance on noble metals and advanced polymer membranes.
Outcome/Impact: Despite its efficiency and versatility, the technology was deemed unviable for large-scale applications, leading GHS to discontinue the PEM electrolyser platform.
.png?width=90&height=224&name=TestingDeployment%20of%20Pressurised%20Alkaline%20Electrolyser%20(14).png)


2016: Testing/Deployment of PEM Electrolyser
Overview: GHS launched the next-generation A-Series system in 2021, offering larger stacks and enhanced performance. Since then, the product has undergone continuous improvements.
Details: The systems' hydrogen production range increased from 30-60 Nm³/h to 90 and later 180 Nm³/h. The system included highly efficient cell stacks delivering hydrogen at 30 bar(g) pressure, a purity of 99.998%, and an efficiency of 53 kWh/kg (stack at 600 mA/cm2).
Outcome/Impact: From 2021 to 2024, the commercial A-Series product has substantially improved in output, reliability, and serviceability, making it a competitive option for hydrogen projects in the 1-4 MW scale.
.png?width=90&height=224&name=TestingDeployment%20of%20Pressurised%20Alkaline%20Electrolyser%20(15).png)


2021-2024: Next generation | A-Series Pressurised Alkaline Electrolyser
Overview: Two years later, GHS tested and deployed its first pressurised alkaline electrolyser in a local pilot project in Denmark.
Details: The system stored wind energy as hydrogen via electrolysis and converted it back into electricity as needed, producing hydrogen at 30 bar(g) and achieving a stack efficiency of 54.7 kWh/kg at 300 mA/cm2.
Outcome/Impact: The pilot project confirmed the efficiency and scalability of the modular and pressurised electrolyser, proving it as a viable on-site solution for clean power.
.png?width=90&height=224&name=TestingDeployment%20of%20Pressurised%20Alkaline%20Electrolyser%20(17).png)


2010: Testing/Deployment of Pressurised Alkaline Electrolyser
Overview: GHS launched its first generation of pressurised alkaline electrolysers. A fully modular containerised, plug-and-play system available in sizes ranging from 20 to 60 Nm³/h.
Details: Operating at 30 bar(g) pressure and consuming 300-320 kW, the A-Series achieved an efficiency of 57 kWh/kg at 400 mA/cm2 with advanced stack design, activated electrodes, high current density, and extended durability.
Outcome/Impact: This first A-series system proved to be a viable and scalable solution and marked a turning point for GHS as a business.
.png?width=90&height=224&name=TestingDeployment%20of%20Pressurised%20Alkaline%20Electrolyser%20(16).png)


2017: Commercial launch | A-series Pressurised Alkaline Electrolyser
Overview: Based on the lessons learned from the A-Series, GHS developed the X-Series, a 6 MW modular, high-pressure electrolyser designed for scale. Development of the solution started in 2021 to address the growing demand for large-scale projects.
Details: Building on the A-series core technology, the X-Series introduces new subsystems to enhance scalability, reliability, and cost-effectiveness. Operating dynamically from 25-100%, it produces up to 1,200 Nm3/h hydrogen at ≥ 35 barg, consuming only 51,9 kWh/kg (stack at 800 mA/cm2.).
Outcome/Impact: The X-series is key to GHS’ growth and scaling ambitions. In anticipation of growing demand, manufacturing capacity has been increased to 400MW annually, and further expansions are in the making. As part of the go-to-market plan, GHS has been running its own 6MW test site since early 2023, continuing to fine-tune and optimise the unit's performance. Finally, partnerships with leading EPCs and integrators throughout Europe have been established to ensure local support with the technical knowledge and know-how required to deliver a good customer experience.
.png?width=90&height=224&name=TestingDeployment%20of%20Pressurised%20Alkaline%20Electrolyser%20(18).png)


2024: Commercial launch | X-Series pressurised alkaline electrolyser
Electrolyser Technologies
Water electrolysis splits water into hydrogen and oxygen using an electrical current. There are various types of water electrolyser technologies available, such as Pressurised Alkaline Water Electrolysis (PAWE), Proton Exchange Membrane (PEM), Alkaline Water Electrolysis (AWE), and Solid Oxide Electrolysis Cell (SOEC). However, when assessing factors such as efficiency, scalability, and reliability, PAWE presents several benefits, making it a compelling choice for large-scale hydrogen production.
AWE
Alkaline Water Electrolysis
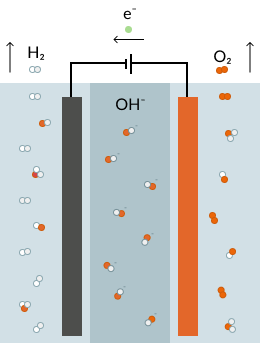
Alkaline Water Electrolysis (AWE): This technology uses an alkaline solution, typically potassium hydroxide, as the electrolyte. The technology traditionally operates at intermediate temperatures and low current density and has established a long-standing presence in the industry.
PAWE
Pressurised Alkaline Water Electrolysis
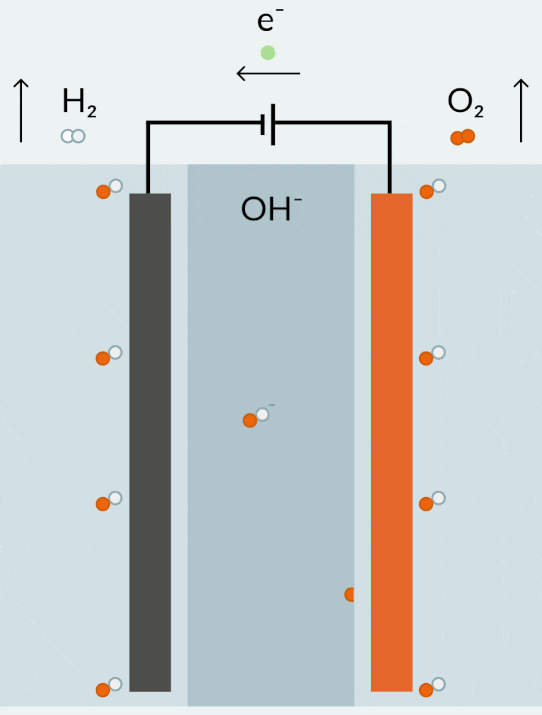
Pressurised Alkaline Water Electrolysis (PAWE): This technology uses electrolysers as pressure vessels, utilising electrochemical reactions to pressurise the system. There are distinct advantages with this approach, as utilising this electrolyser can effectively reduce the overall energy demand for producing pressurised hydrogen. This means that the pressurised system can operate at higher current densities while keeping the overall size down.
PEM
Proton Exchange Membrane
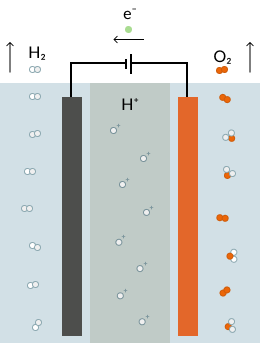
Proton Exchange Membrane Electrolysers (PEM): This technology uses a solid polymer membrane as its electrolyte, commonly composed of a proton-conductive material such as perfluorosulfonic acid. The technology depends on noble metals, such as iridium and platinum, to manufacture the PEM electrolyser.
SOEC
Solid Oxide Electrolysis
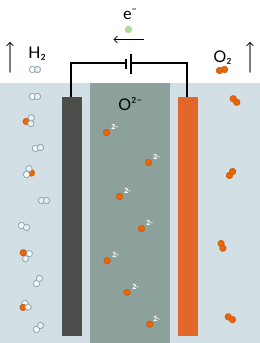
Solid Oxide Electrolyser Cell (SOEC): This technology employs a solid ceramic electrolyte, such as yttria-stabilised zirconia, which conducts oxygen ions at high temperatures, typically exceeding 500 °C. This places stringent requirements on the materials used to achieve a satisfactory lifespan for the components.
Our team is standing by to answer all of your questions about pressurised alkaline electrolysis technology, electrolysers, or green hydrogen. You can reach us anytime using the button below or hovering to the right.
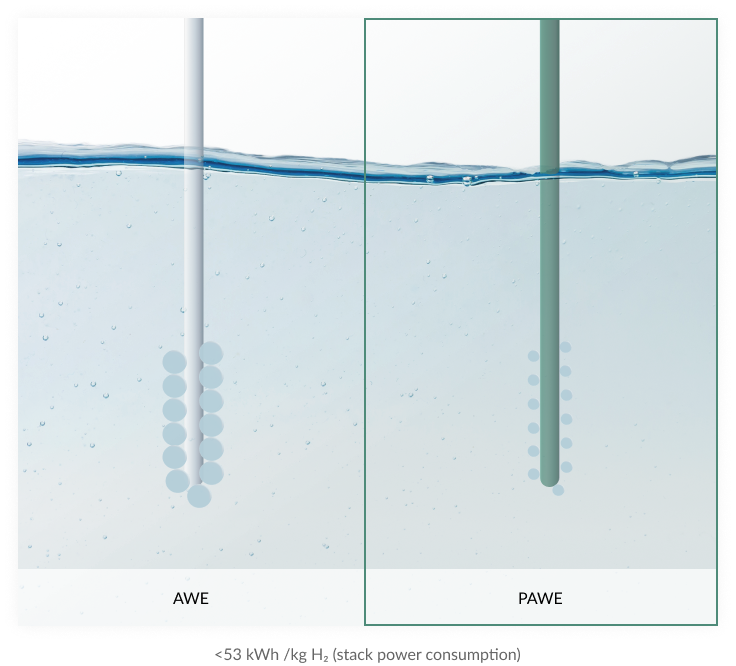
HOW DOES PRESSURISED ALKALINE WATER ELECTROLYSIS WORK?
The PAWE system works like a traditional AWE system in the way that it uses a liquid alkaline electrolyte solution; it differs from AWE by using the stack and Balance-of-Plant (BoP) to pressurise the produced gases (hydrogen and oxygen) by preventing the release of the gases from the BoP until the system reaches the desired pressure. The increased system pressure has two distinct positive influences on performance. First, the pressure ensures that the gas bubbles formed on the electrodes will take up less space on the electrode surface, i.e., freeing space for more reaction sites, which equals better efficiency. Second, The volume of the produced gas will be smaller, making the electrolyte more conducting, which equals better efficiency.
This means that compared to an AWE system, PAWE systems can be operated at higher current density (higher production rate) at the same efficiency or with the same production rate at a higher efficiency.
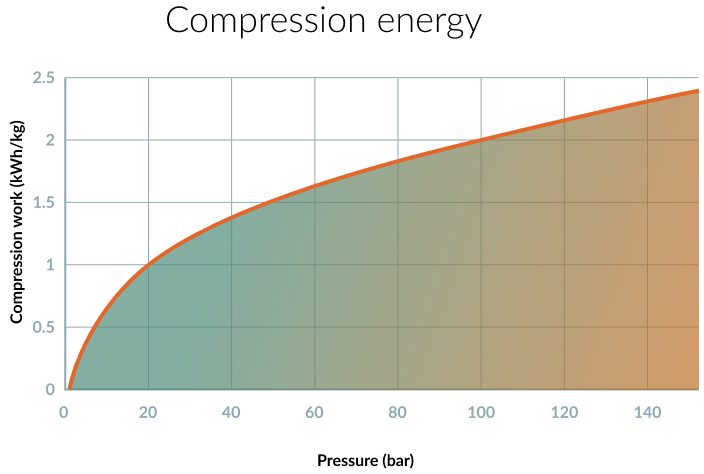
Having a pressurised alkaline electrolyser offers several specific advantages. One notable benefit is the reduction in overall CAPEX and OPEX costs. By utilising the cell stack as a pressure vessel, PAWE can effectively reduce the costs of the compression equipment needed in the hydrogen production line, and this is particularly significant when considering the energy required to compress hydrogen gas. It is important to note that the process is most cost-intensive within the lower pressure range, specifically up to 30 bar.
To minimise the space required for an electrolyser system, it is important to build up pressure early in the process. This reduces the volume of gas and optimises the efficiency of the system. By taking advantage of the cell stack's ability to act as a pressure vessel, we can make the hydrogen production process more cost-effective, energy-efficient and compact.
PROVIDES DYNAMIC OPERATIONAL SUPPORT
Electrolysers built on pressurised alkaline water technology provide dynamic operational support, making them suitable for intermittent, renewable power sources and energy storage applications, and this represents a significant difference from atmospheric alkaline systems that lack the capability to facilitate swift ramp-up and ramp-down processes.
In a +30 bar pressurised alkaline water system, the gas is compressed and takes up a smaller volume relative to the liquid volume, making it much easier to maintain balance in the system. The limitation of atmospheric systems during a ramp-up is that the gas takes up a significantly larger volume, and this makes these systems less capable of handling spiking gas volumes within the stack cells because it compromises the critical need for electrolyte supply to the stack, providing reactants, conductivity, and often also cooling.
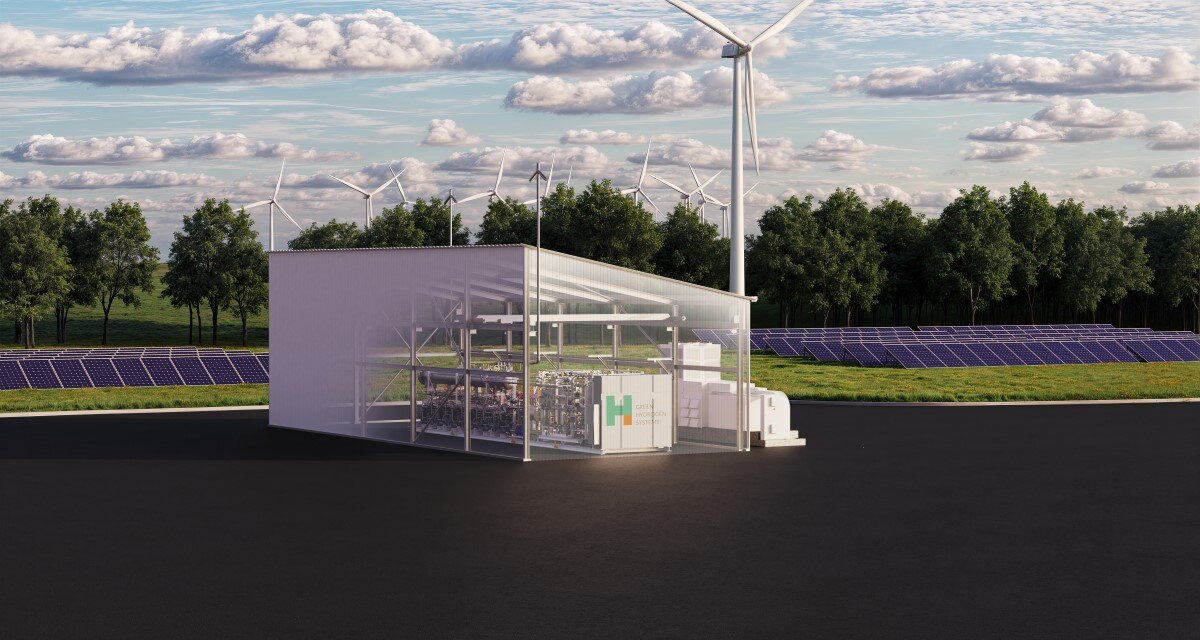
Did you know?
GHS offers more than just stacks. We provide integrated electrolyser units - designed, assembled, and tested in-house. This has several advantages:
- Minimises on-site assembly and installation time
- Reducing project risk with factory-tested units.
- Ensures full integration of the BOP and stack.
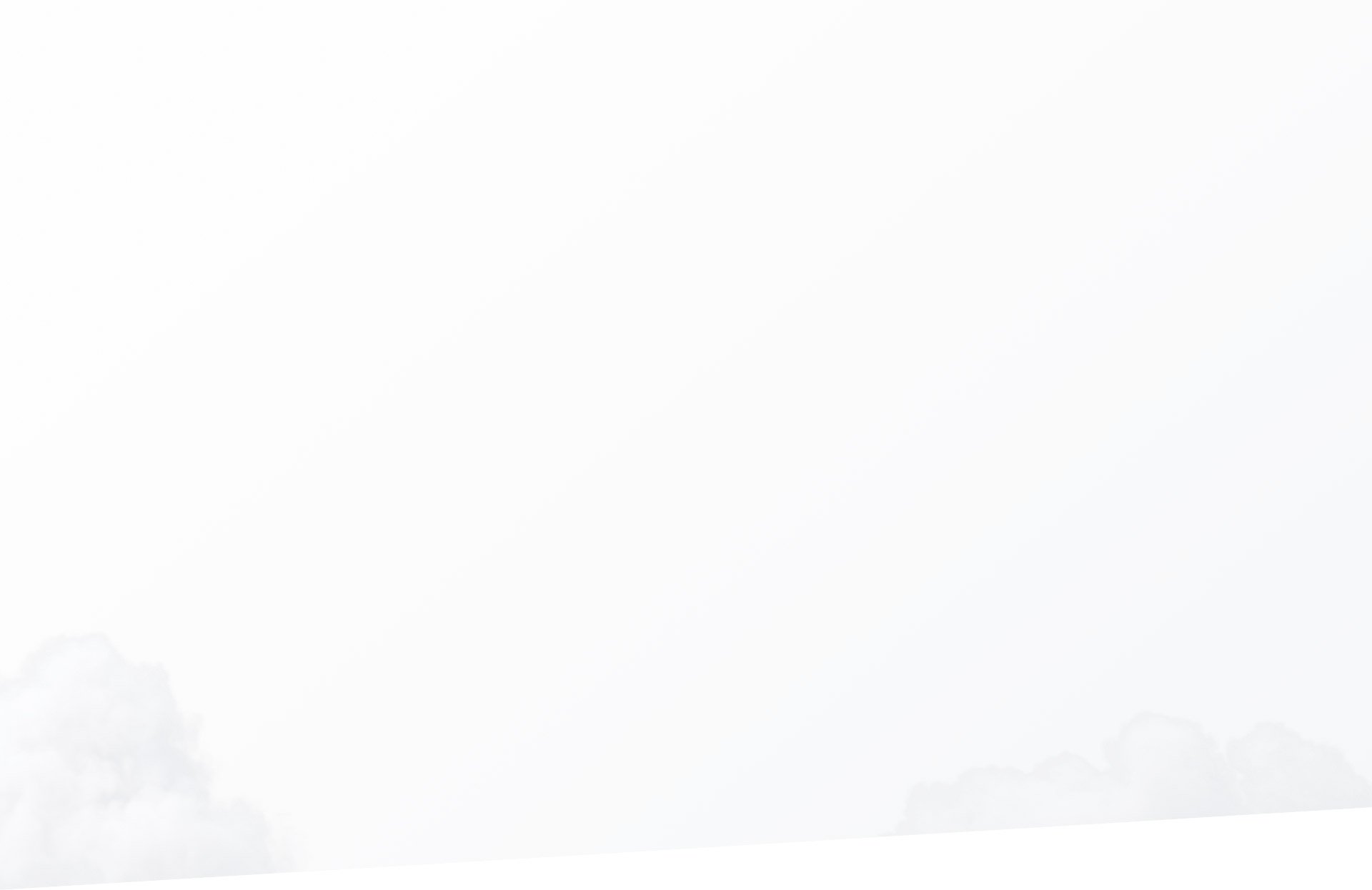
ADVANTAGES OF PRESSURISED ALKALINE
WATER ELECTROLYSIS?
Pressurised alkaline water technology combines the key advantages of Proton Exchange Membrane (PEM) and Alkaline Water Electrolysis (AWE). This technology suits rapid scale-up, clustered solutions, and serial production. It offers a long stack lifetime, flexibility, low water purity requirements and a small product footprint. By integrating the strengths of PEM and AWE, pressurised alkaline water technology showcases its versatility and efficiency, making it a game-changer in sustainable energy production.
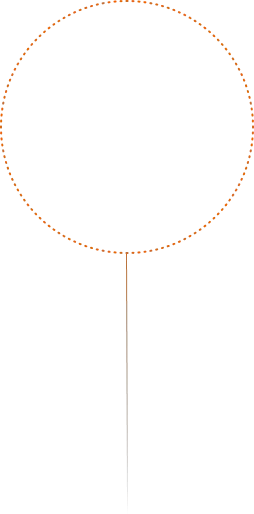
Long Stack Lifetime: Competitive energy to hydrogen conversion
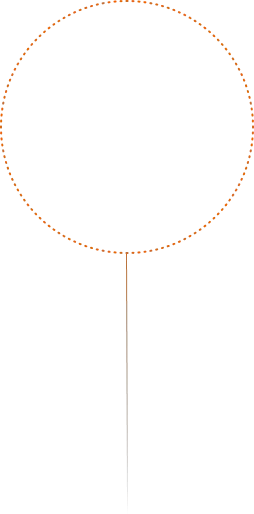
Flexibility: Capacity to operate dynamically at variable load levels
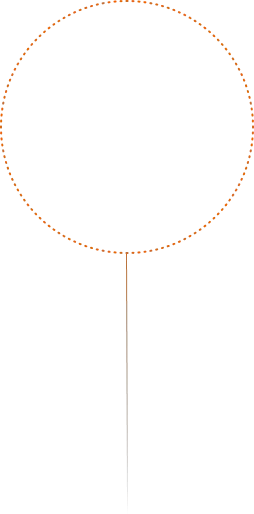
30+ barg hydrogen output pressure allowing for a small product footprint
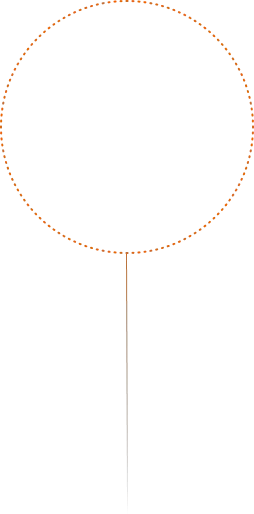
Low purity requirements for process feed water

The HyProvide® X-1200 System
The technology described above makes the HyProvide® X-1200 one of today’s most efficient green hydrogen electrolysers. The X-1200 is available in standardised, modular configurations for maximum efficiency, versatility, and scalability. Furthermore, the units can operate independently or in clusters to produce the required volume of green hydrogen on a multi-MW scale.
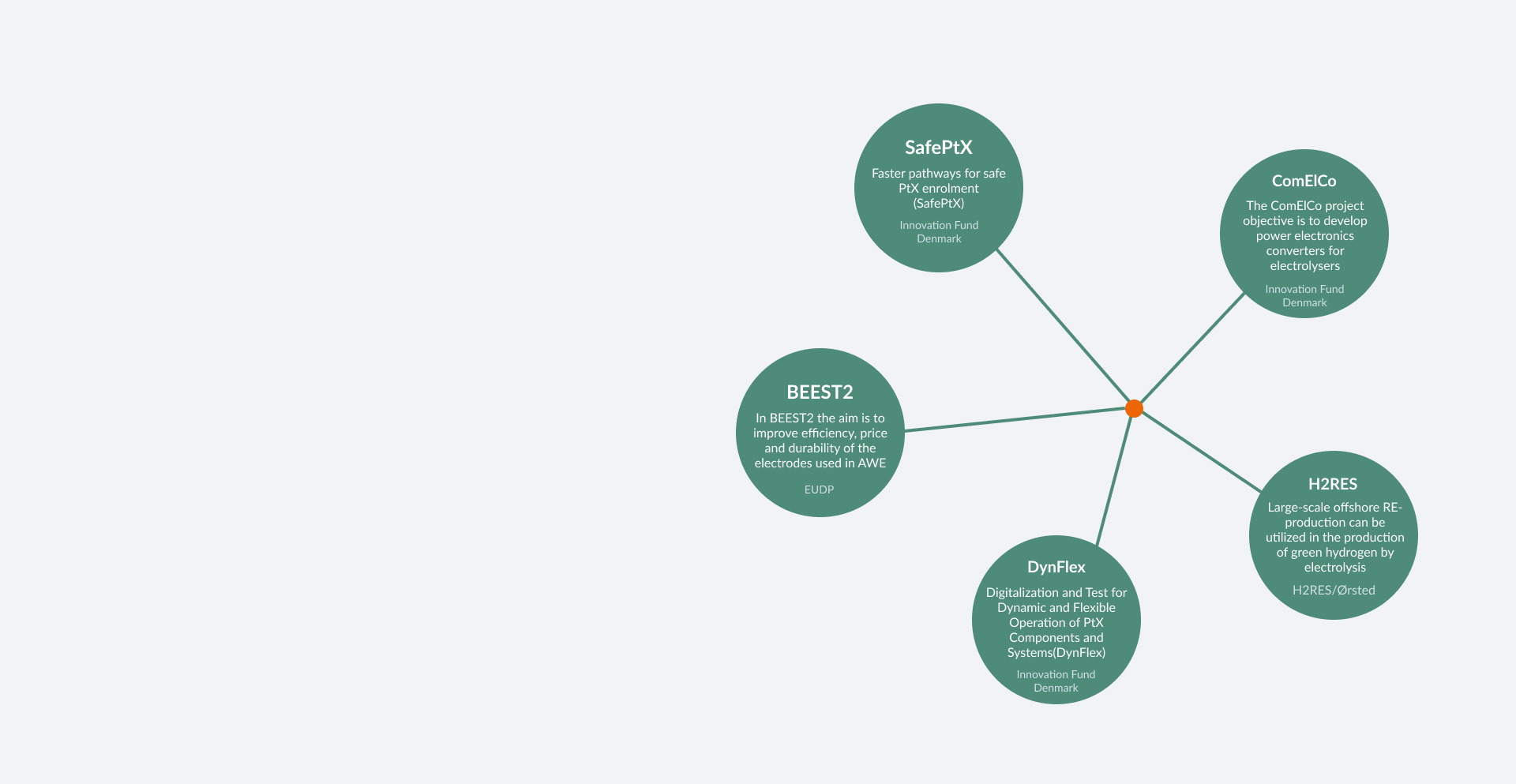
Advances in technology and innovation
Green Hydrogen Systems (GHS) is dedicated to improving our technology to provide cleaner and more sustainable energy solutions. To achieve this goal, GHS actively participates in several research projects within Denmark and the European Union, including:
- ComElCo, which aims to develop power electronics converters for electrolysers with improved efficiency, low cost, and provisions for grid services. ComElCo develops power converters and, together with the stacks, will be able to improve system efficiency. Read more
- BEEST2, which aims to develop and demonstrate a next-generation alkaline water electrolyser stack with improved efficiency, durability, and price. It will use new combinations of materials and processing techniques to enhance electrodes and internal components. Read more
- DynFlex, setting out to develop new methods for dynamic modelling, testing, and flexible operation of individual PtX components and systems, supporting scale-up, business cases, and technology platforms for producing green fuels. Read more.
These collaborative efforts allow GHS to stay at the forefront of technology and continuously innovate its electrolysers.
We believe that green hydrogen will be at the heart of the future energy system, and we are committed to being on the forefront of that global transition.